

PSM / EPA
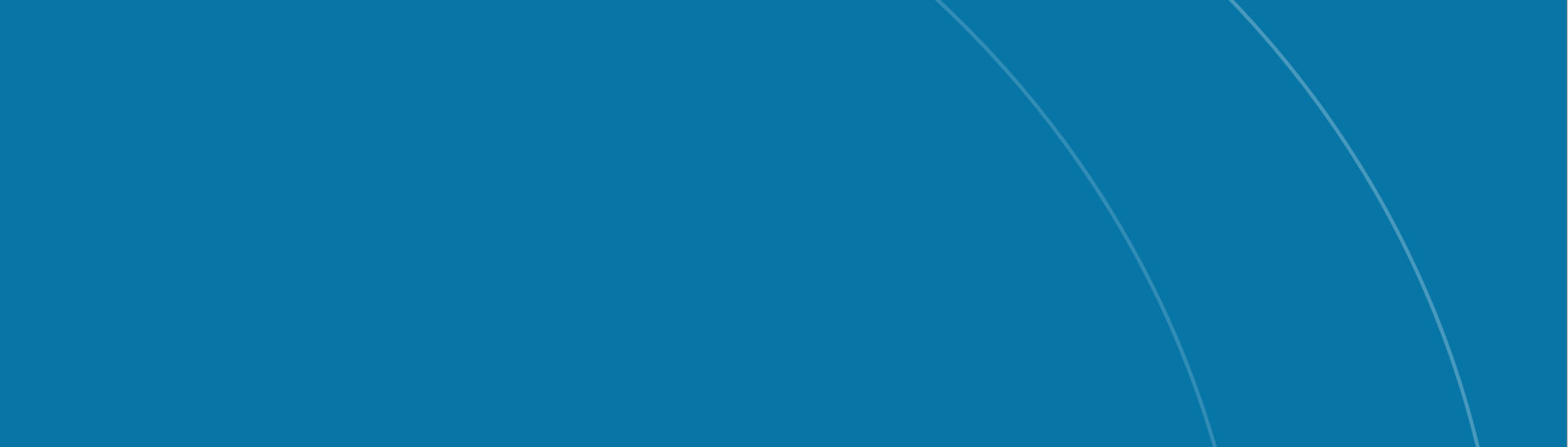
Our foremost goal at every industrial refrigeration facility, is employee and public safety. Helping you navigate the Process Safety Management (PSM) and Environmental Protection Agency (EPA) requirements is essential to ensure the safe operation of your systems, particularly those using ammonia and other hazardous chemicals.
PSM, mandated by OSHA, involves a comprehensive approach to preventing the release of dangerous substances. Our PSM programs cover all 14 key areas. These elements work together to identify, analyze, and control potential hazards, creating a safer work environment for everyone.
In addition to PSM, we undestand and can help you comply with the EPA’s Risk Management Program (RMP). This program focuses on preventing and mitigating the effects of chemical accidents that could impact public health and the environment. Our RMP includes a management system to oversee safety activities, detailed hazard assessments to understand potential risks, and a five-year accident history to learn from past incidents.
Here for You
Put our century of experience to work for you and your facility. Big or small, near & far – we’re here to help.
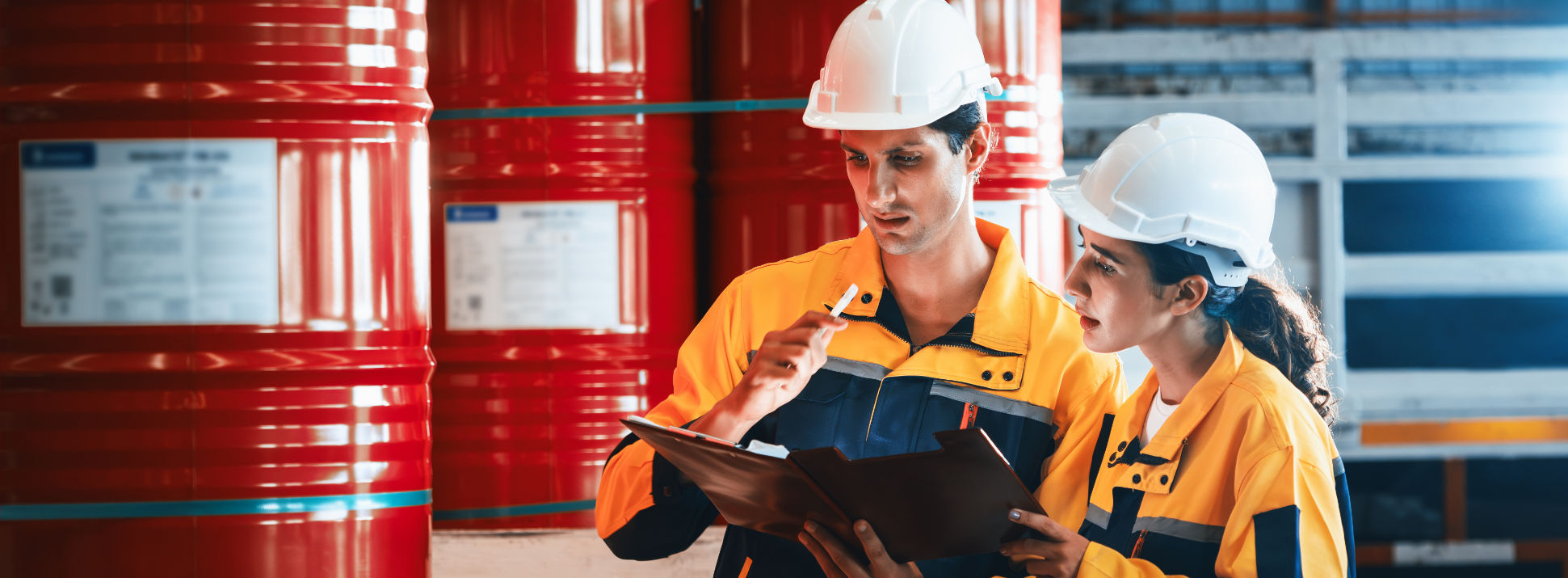
PSM

Process Safety Management
1. Employee Participation
- Encourages the involvement of employees in the development and implementation of PSM programs.
- Ensures employees have access to process safety information and can contribute to safety discussions.
- Promotes a safety culture where workers feel empowered to report safety concerns and suggest improvements.
2. Process Safety Information
- Involves compiling detailed information on the hazardous chemicals, technology, and equipment used in processes.
- Ensures that safety data sheets (SDS), chemical hazard information, and process descriptions are up-to-date and accessible.
- Includes information on maximum intended inventory, safety systems, and equipment design specifications.
3. Process Hazard Analysis (PHA)
- A systematic approach to identifying and analyzing potential hazards associated with industrial processes.
- Utilizes methods like HAZOP (Hazard and Operability Study), FMEA (Failure Modes and Effects Analysis), and What-If analysis.
- Aims to identify weaknesses in the process design and operation that could lead to accidents.
4. Operating Procedures
- Establishes clear and concise instructions for safely conducting activities involved in process operations.
- Includes startup, shutdown, normal operations, emergency operations, and temporary operations procedures.
- Ensures that procedures are regularly reviewed and updated to reflect current practices and changes.
5. Training
- Provides comprehensive training to employees on the specific hazards of their job and the proper use of safety equipment.
- Ensures that employees understand operating procedures and the PSM program.
- Includes refresher training at regular intervals and competency
6. CONTRACTORS
- Ensures that contractors are informed about the potential hazards of their work environment.
- Requires contractors to follow safety procedures and comply with the host employer’s PSM program.
- Involves evaluating contractor safety performance and maintaining communication during projects.
7. Pre-Startup Safety Review (PSSR)
- Conducts a thorough review of safety systems, procedures, and equipment before starting up a new or modified process.
- Ensures that safety, design, and operational requirements are met.
- Verifies that employees are trained and that procedures are in place before initiating operations.
8. Mechanical Integrity
- Involves the maintenance, inspection, and testing of process equipment to ensure it operates safely.
- Covers pressure vessels, storage tanks, piping systems, relief systems, emergency shutdown systems, and controls.
- Includes regular inspections, preventive maintenance, and prompt repairs to maintain equipment integrity.
9. Hot Work
- Controls activities involving open flames or heat-producing operations, such as welding and cutting.
- Requires hot work permits to ensure safety measures are in place before work begins.
- Includes monitoring and controlling the environment to prevent ignition of flammable materials.
10. Management of Change (MOC)
- Manages changes to process chemicals, technology, equipment, procedures, and personnel that could affect safety.
- Involves evaluating the safety impact of changes before implementation.
- Ensures that affected employees are informed and trained on changes.
11. Incident Investigation
- Investigates incidents that resulted in or could have resulted in a major accident.
- Identifies root causes and contributing factors to prevent recurrence.
- Involves documenting findings, implementing corrective actions, and sharing lessons learned.
12. Emergency Action Plan and Emergency Response Program
- Develops and implements plans for responding to emergencies such as fires, explosions, and chemical releases.
- Includes procedures for evacuation, communication, and coordination with emergency responders.
- Ensures regular drills and training to prepare employees for emergencies.
13. Compliance Audits
- Conducts regular audits to ensure adherence to PSM program requirements.
- Identifies deficiencies and areas for improvement in the PSM system.
- Involves corrective actions to address audit findings and enhance process safety.
14. Trade Secrets
- Protects confidential business information while ensuring it does not compromise safety.
- Balances the need to keep proprietary information confidential with the need to provide sufficient information for safe operation.
- Involves sharing necessary information with employees, contractors, and emergency responders under confidentiality agreements when required.
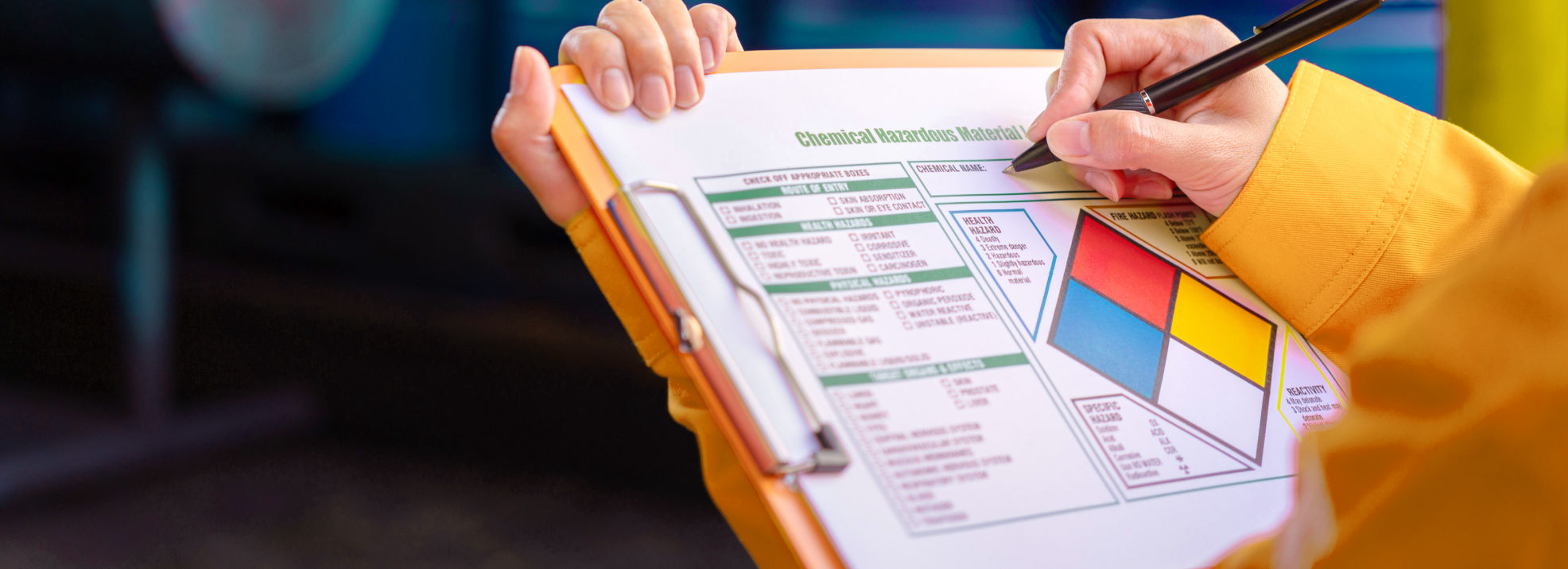
EPA RMP

Rish Management Program
1. Management System
- Purpose: Establishes a structured framework to ensure effective implementation and oversight of the Risk Management Program.
- Components:
- Leadership and Accountability: Designates qualified individuals responsible for the development, implementation, and integration of the risk management program elements.
- Organizational Structure: Defines roles and responsibilities, ensuring all levels of the organization understand their part in maintaining process safety and compliance.
- Documentation and Communication: Ensures that risk management policies, procedures, and responsibilities are clearly documented and communicated to all relevant personnel.
- Continuous Improvement: Implements regular reviews and updates of the management system to incorporate lessons learned, audit findings, and industry best practices.
2. Hazard Assessment for Offsite Consequence Analysis
- Purpose: Evaluates the potential impact of accidental chemical releases on the surrounding community and environment.
- Components:
- Worst-case Scenarios: Identifies the worst-case release scenarios for each regulated substance, considering factors like maximum quantity held, failure of safety systems, and meteorological conditions.
- Alternative Release Scenarios: Analyzes more likely release scenarios that could occur under different conditions, including equipment failures, human errors, and operational deviations.
- Offsite Consequences: Assesses the potential effects of chemical releases on public health, safety, and the environment, including impacts on nearby populations, ecosystems, and critical infrastructure.
- Public Communication: Provides information to the public about potential risks and safety measures, ensuring transparency and community awareness.
3. Five-Year Accident History
- Purpose: Documents and analyzes accidents involving regulated substances that have occurred over the past five years to identify trends, root causes, and areas for improvement.
- Components:
- Accident Documentation: Records details of each accident, including date, location, substances involved, consequences, and immediate response actions.
- Cause Analysis: Investigates root causes and contributing factors of each incident to understand why it occurred and how similar incidents can be prevented.
- Corrective Actions: Implements measures to address identified causes and prevent recurrence, including changes to procedures, equipment, training, and safety systems.
- Reporting and Review: Ensures that accident history is regularly reviewed and reported to relevant authorities and stakeholders, facilitating continuous improvement and regulatory compliance.
Ready to
work with us?
Testimonials
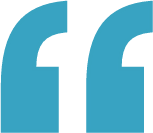
The Louis A. Roser Company is the preferred choice of the Salt Lake City Costco Depot for a wide range of projects including a recent expansion with energy efficient measures and an upgraded control system. Please click on the photo on the right to see more photos and a detailed description of this project.

Costco