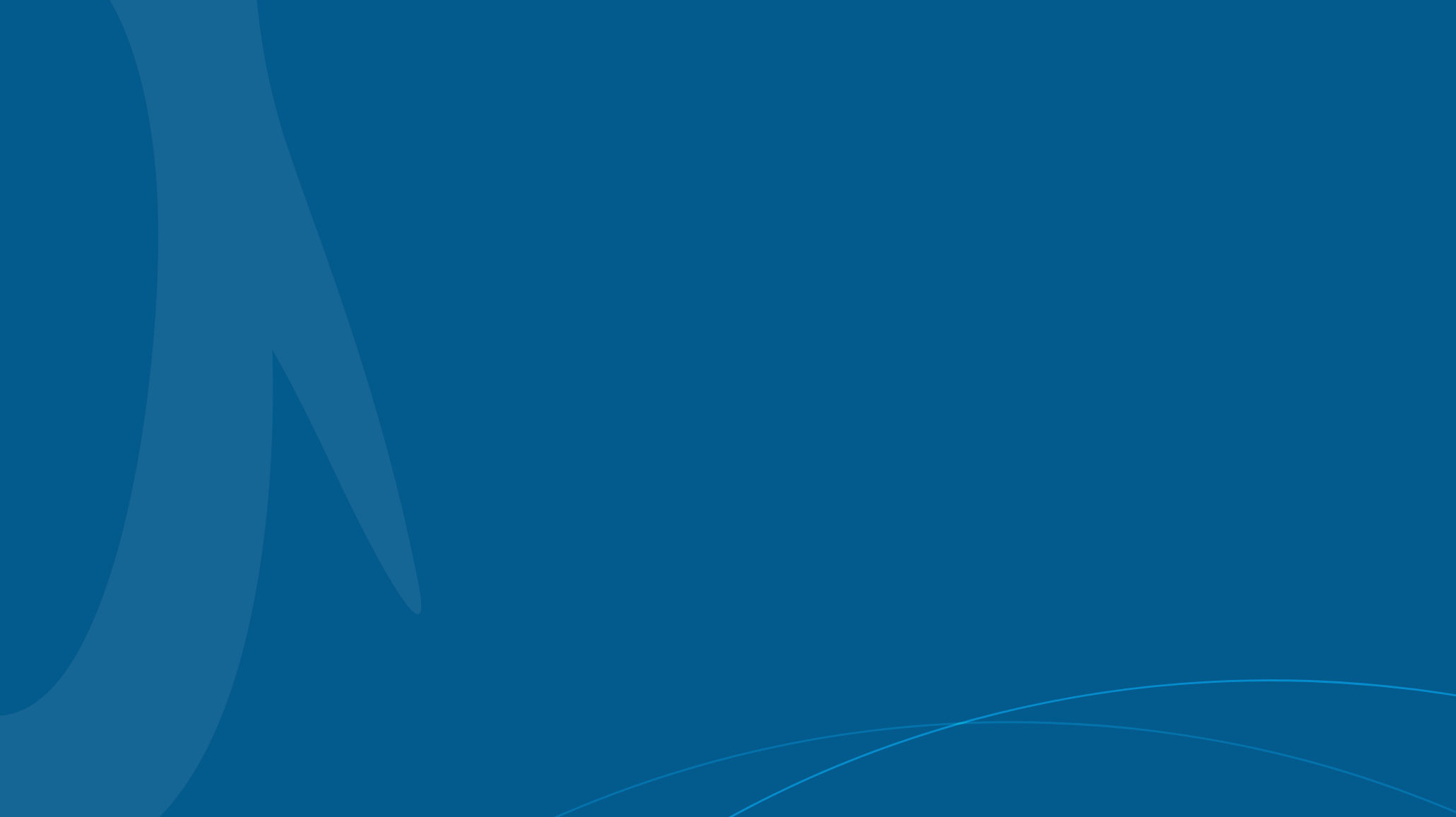
In the early 1900s, Louis A. Roser founded a small business that would grow into a remarkable legacy, spanning four generations. This legacy was carried forward by his son, Glen Roser Sr., and later by his grandson, Glen Roser Jr. Today, the family torch is still carried by Bart Roser, who continues to uphold the values and vision that began over a century ago.
We’re thrilled to share our story with you, showcasing the rich history of our journey. Below, you’ll find a collection of photos from our past that offer a glimpse into our heritage. We hope you enjoy this visual journey, and stay tuned for more photos and stories in the future, as we continue to celebrate our legacy.
Today we believe in blending tradition with forward-thinking technologies to meet the evolving needs of our clients.
Founded on the principles of integrity, innovation, and unparalleled customer service, we have consistently delivered high-performance solutions across industries.
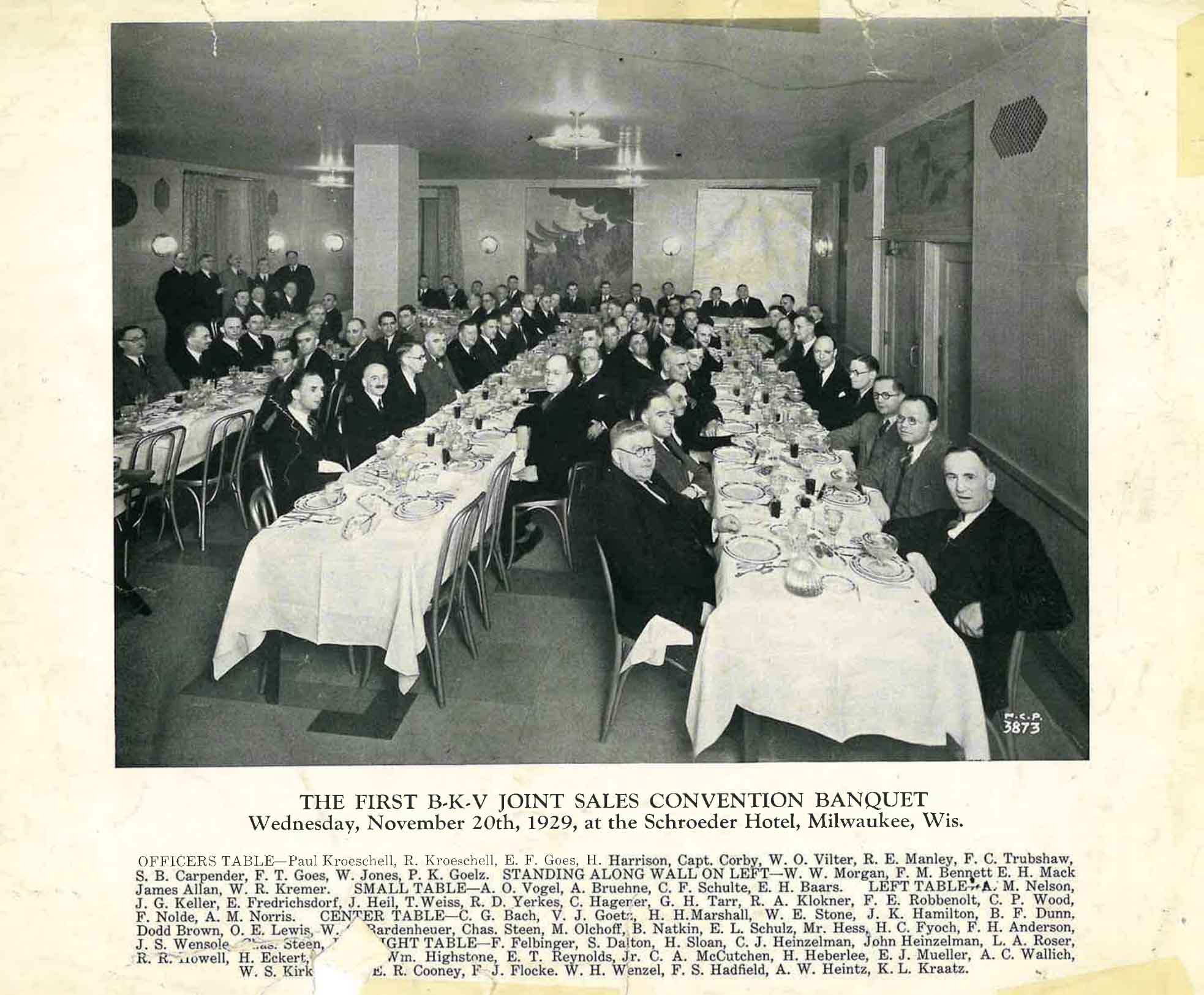
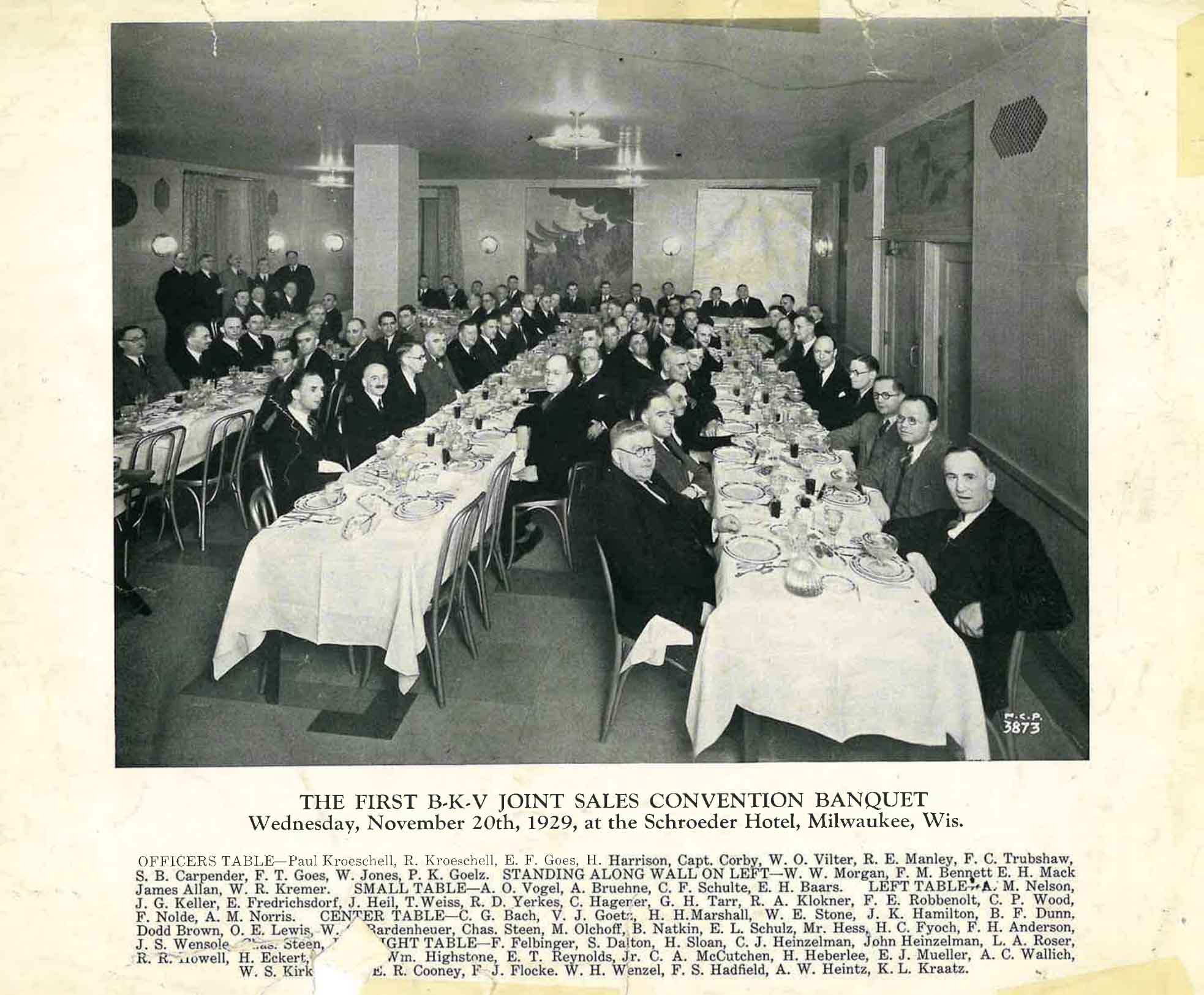
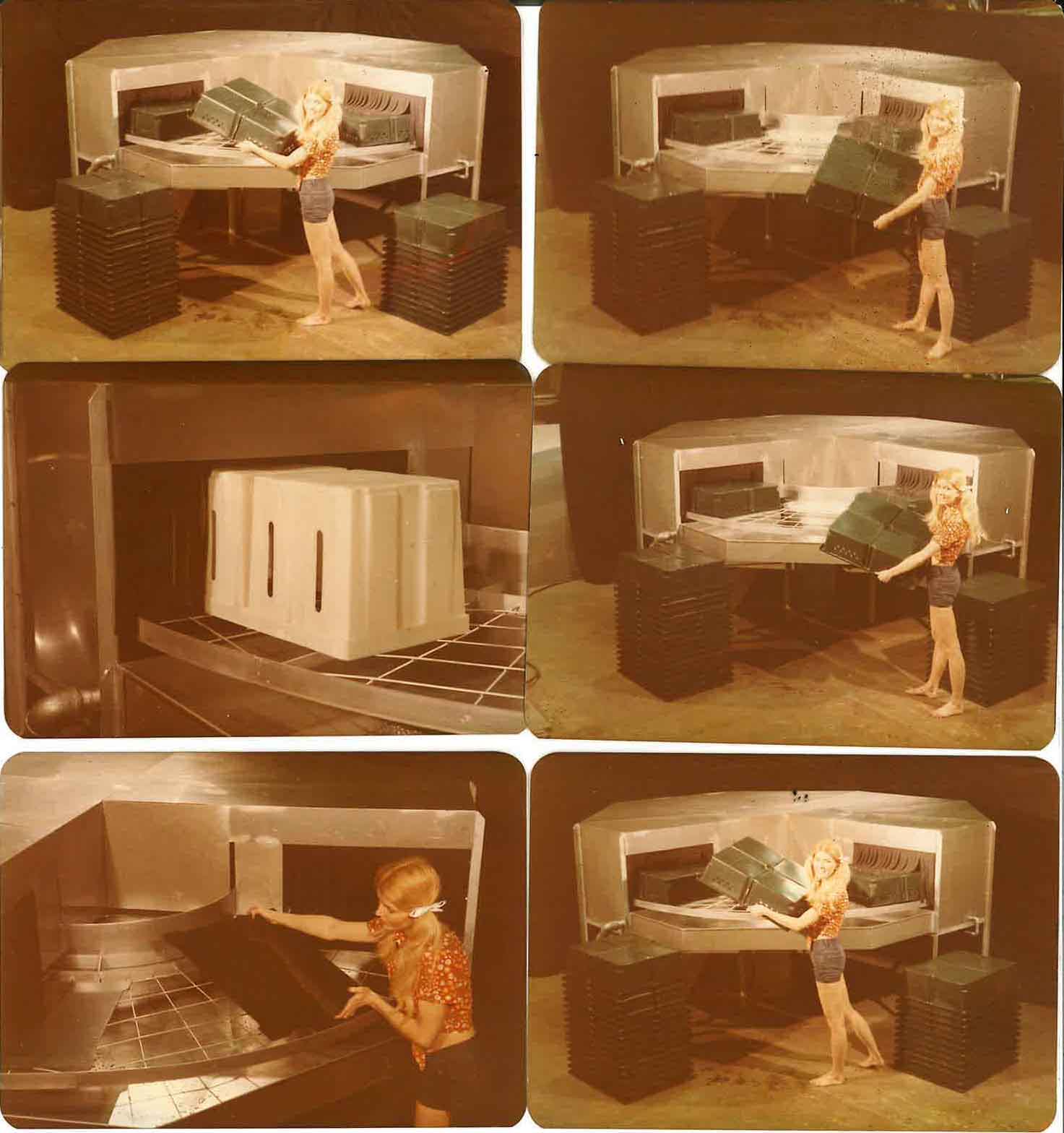
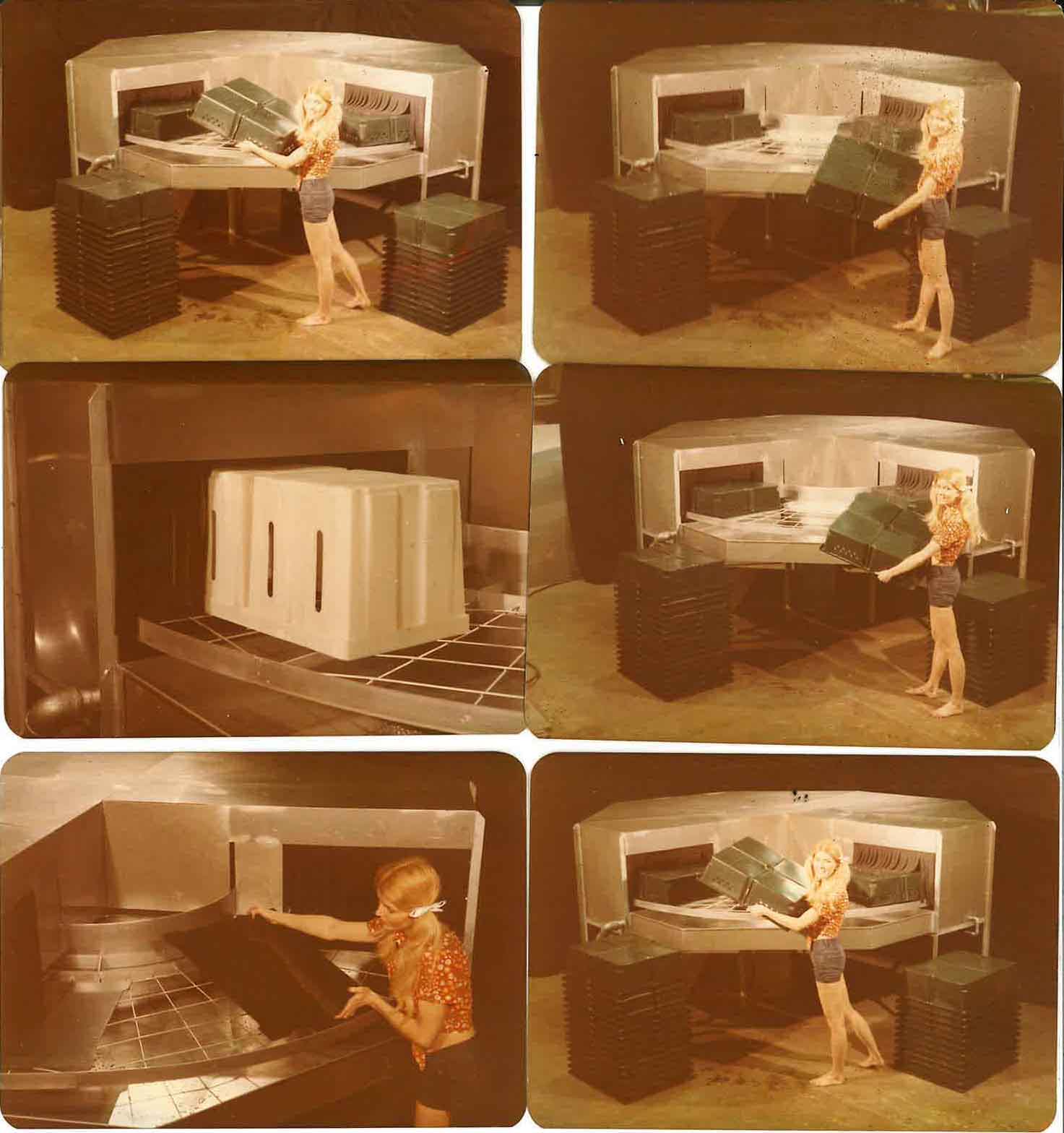
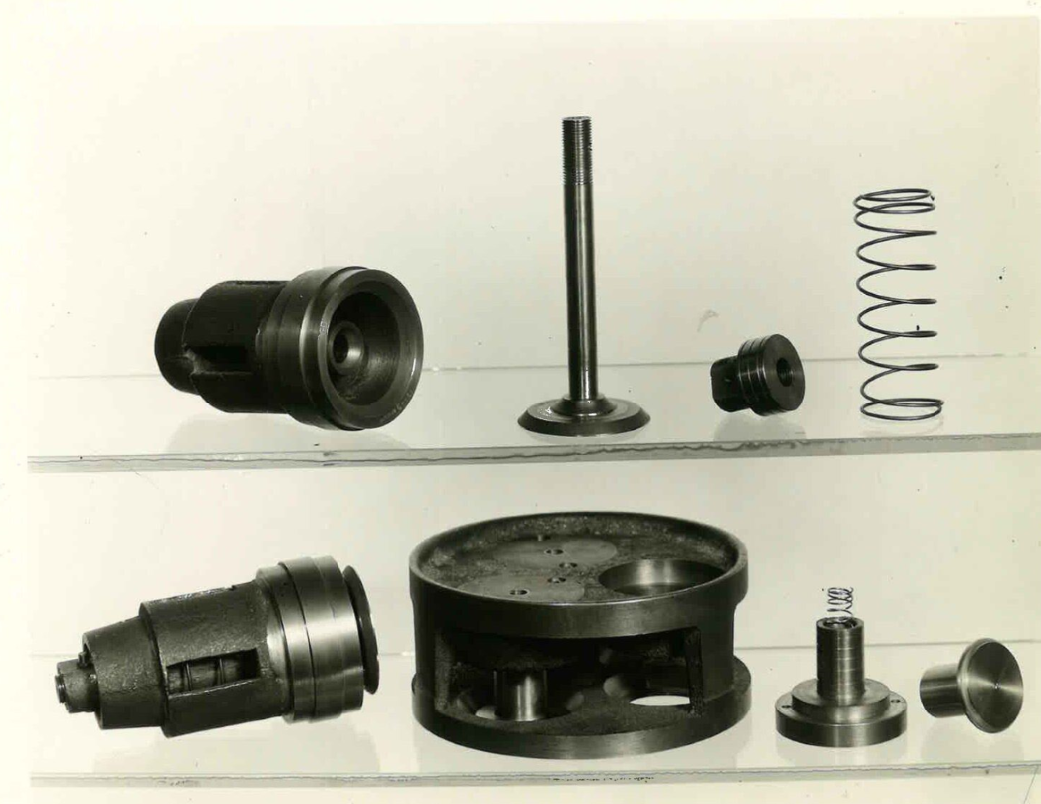
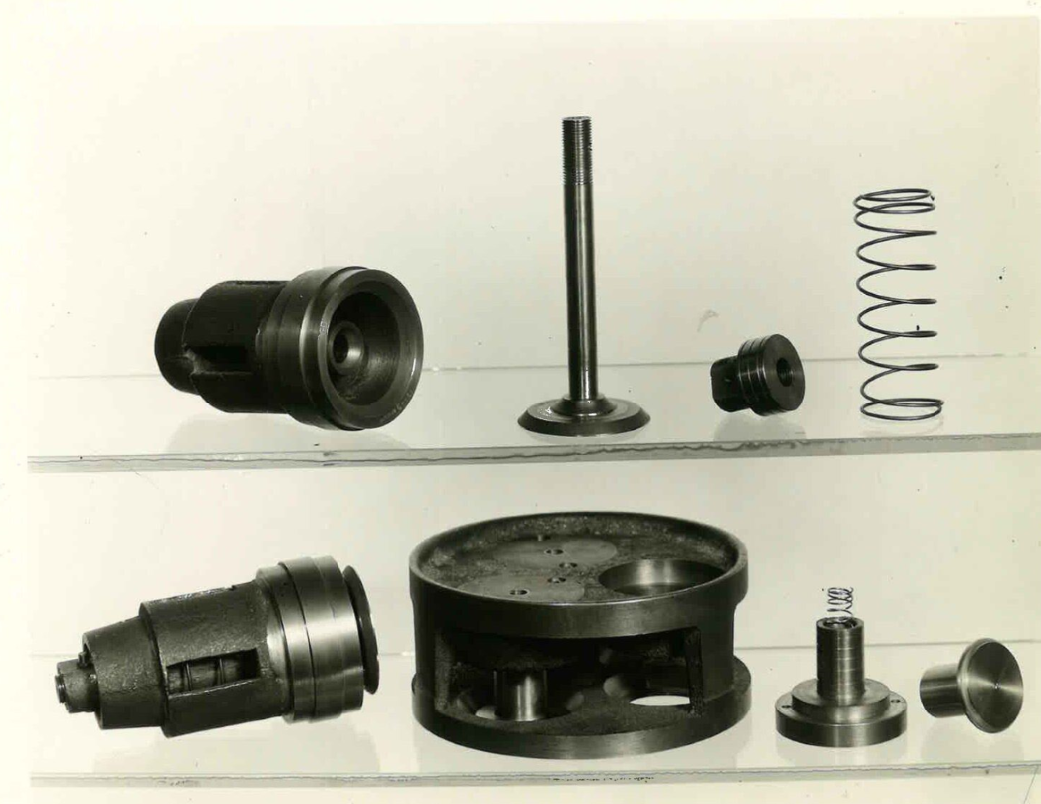
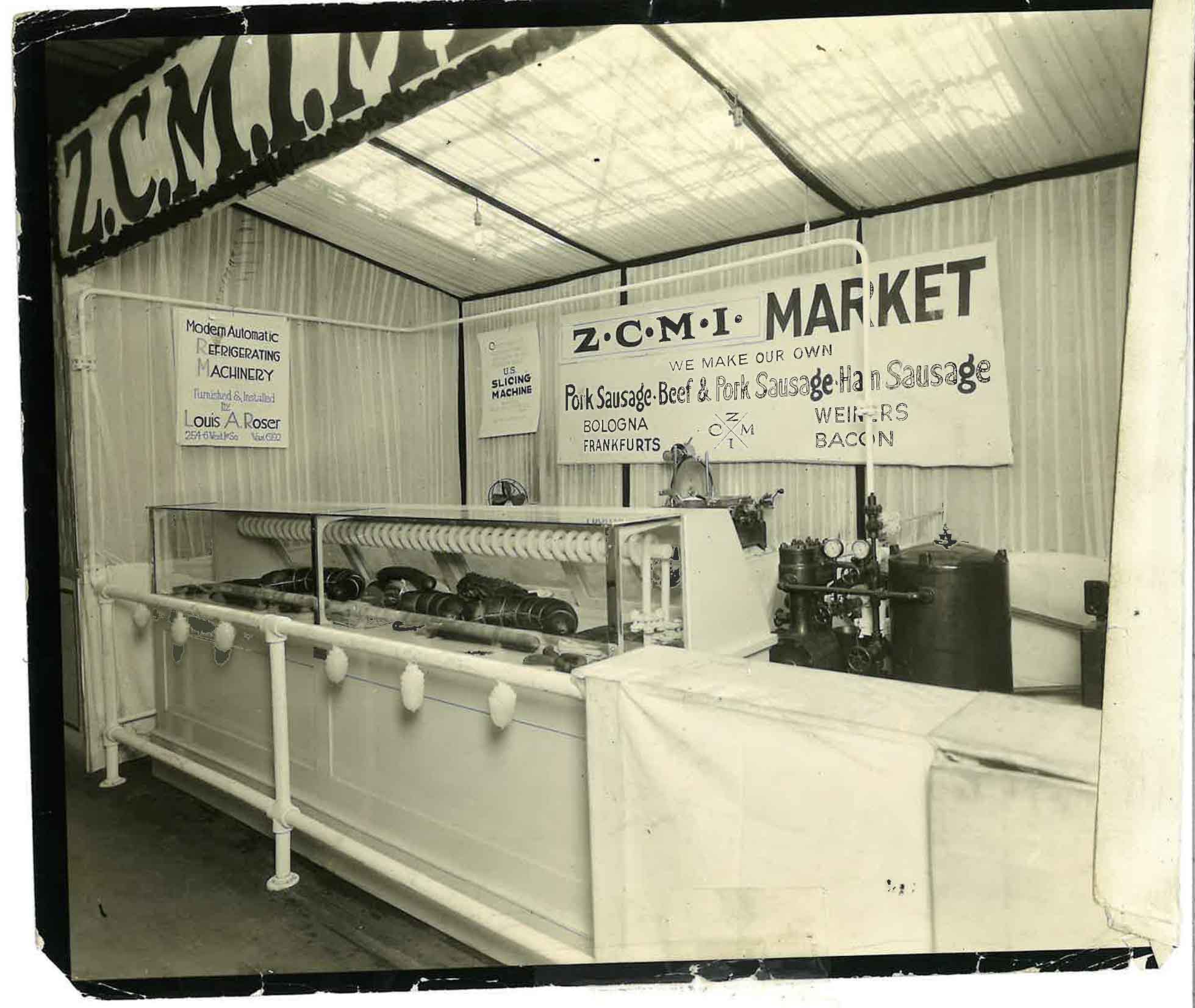
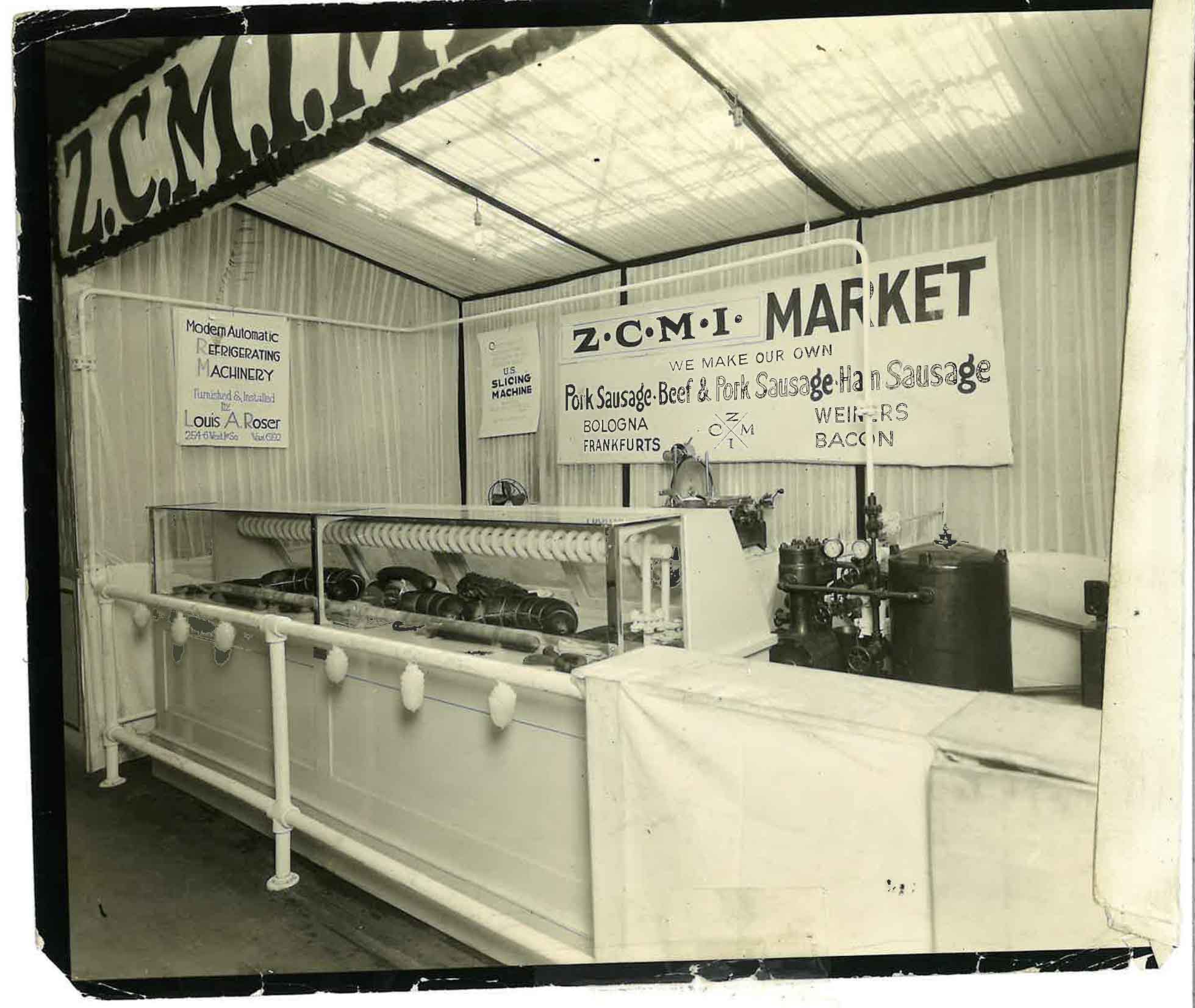
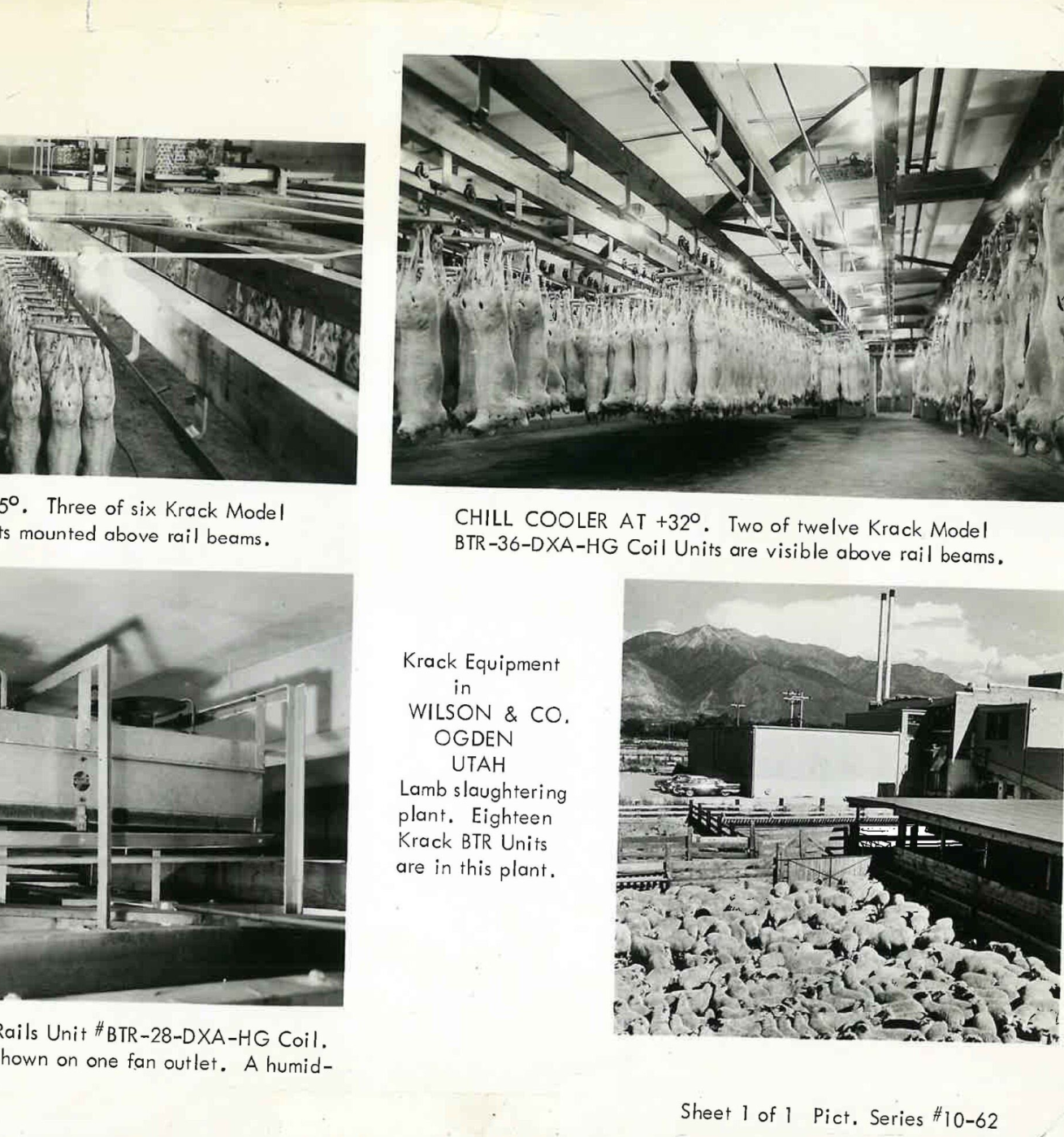
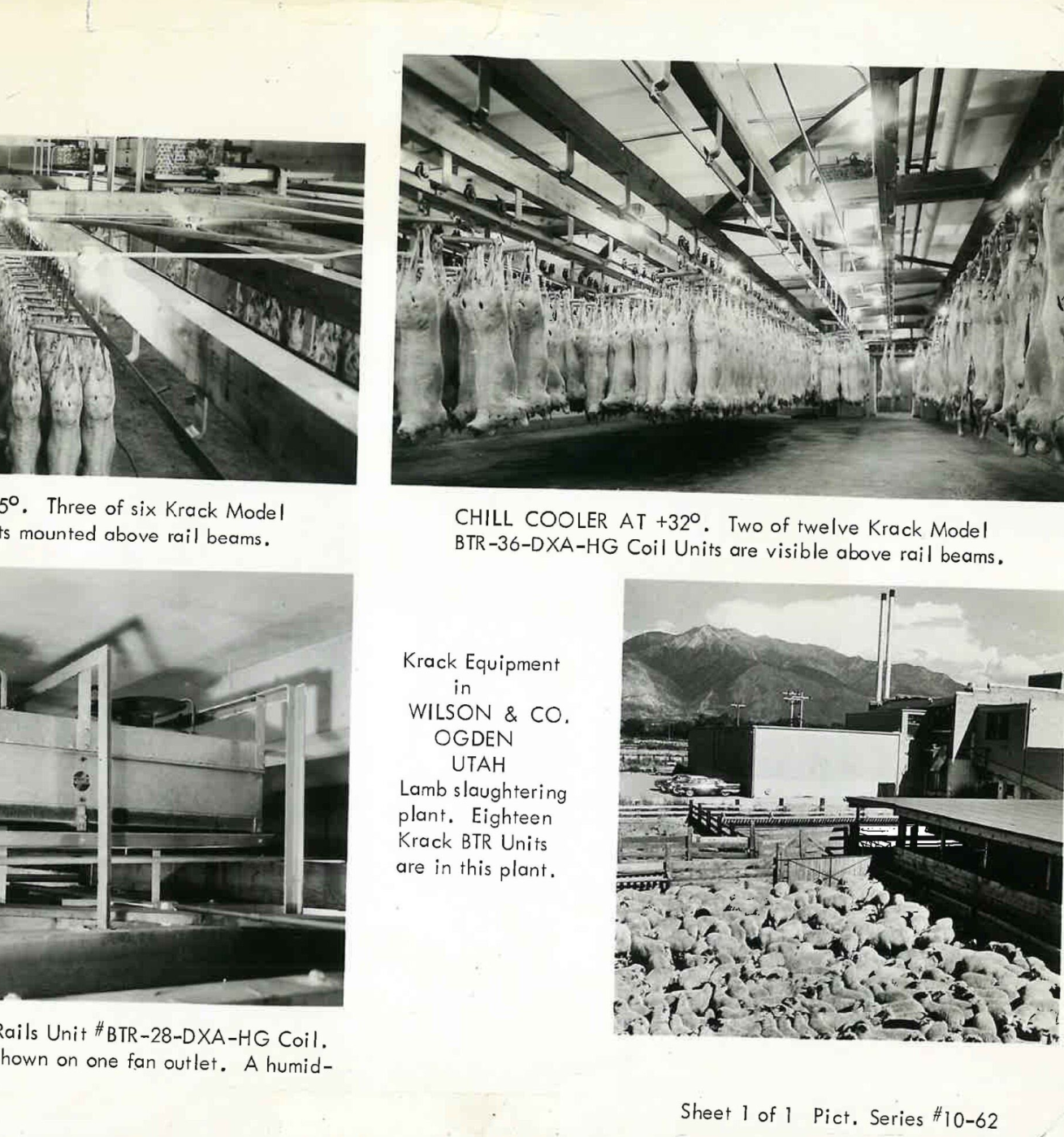
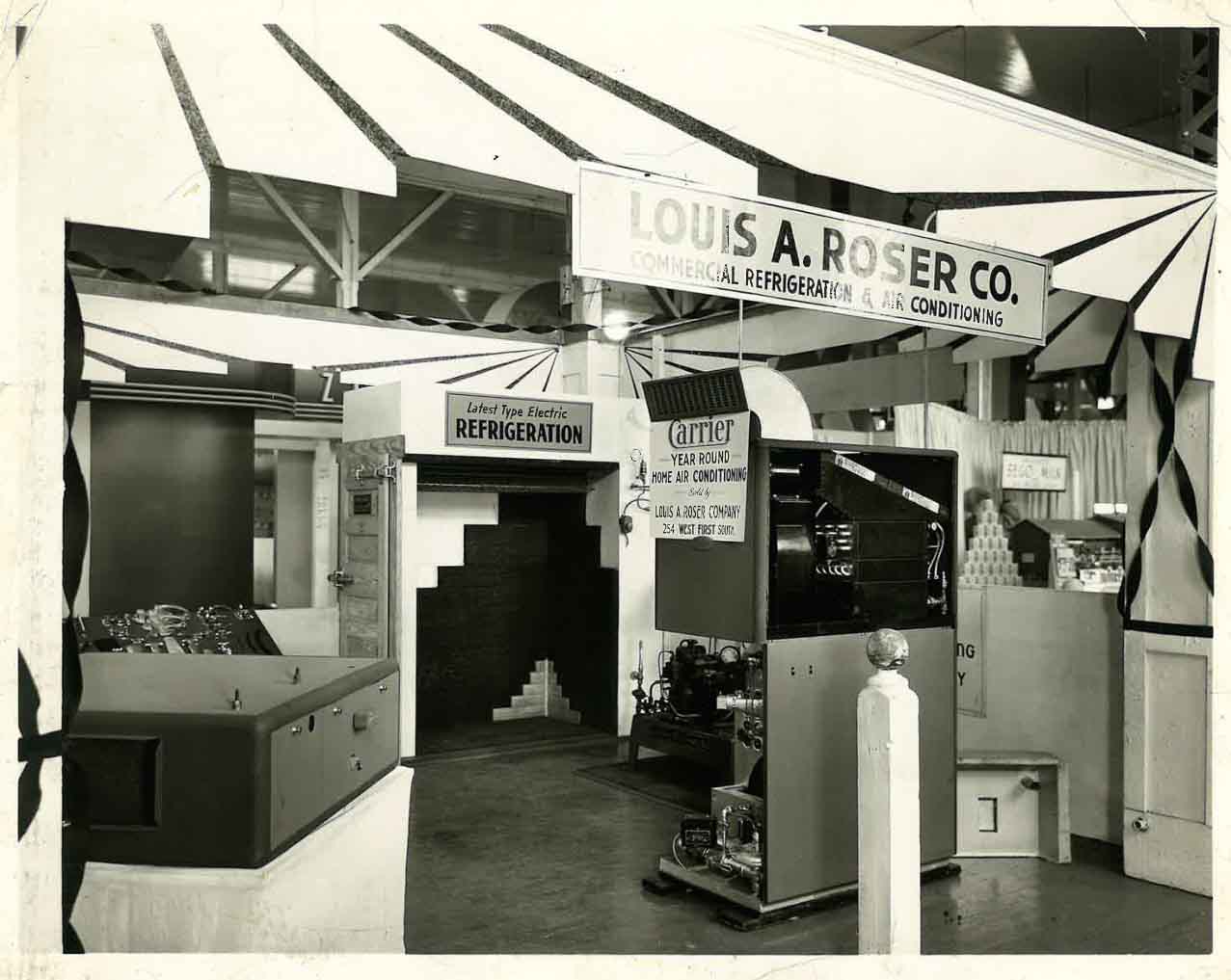
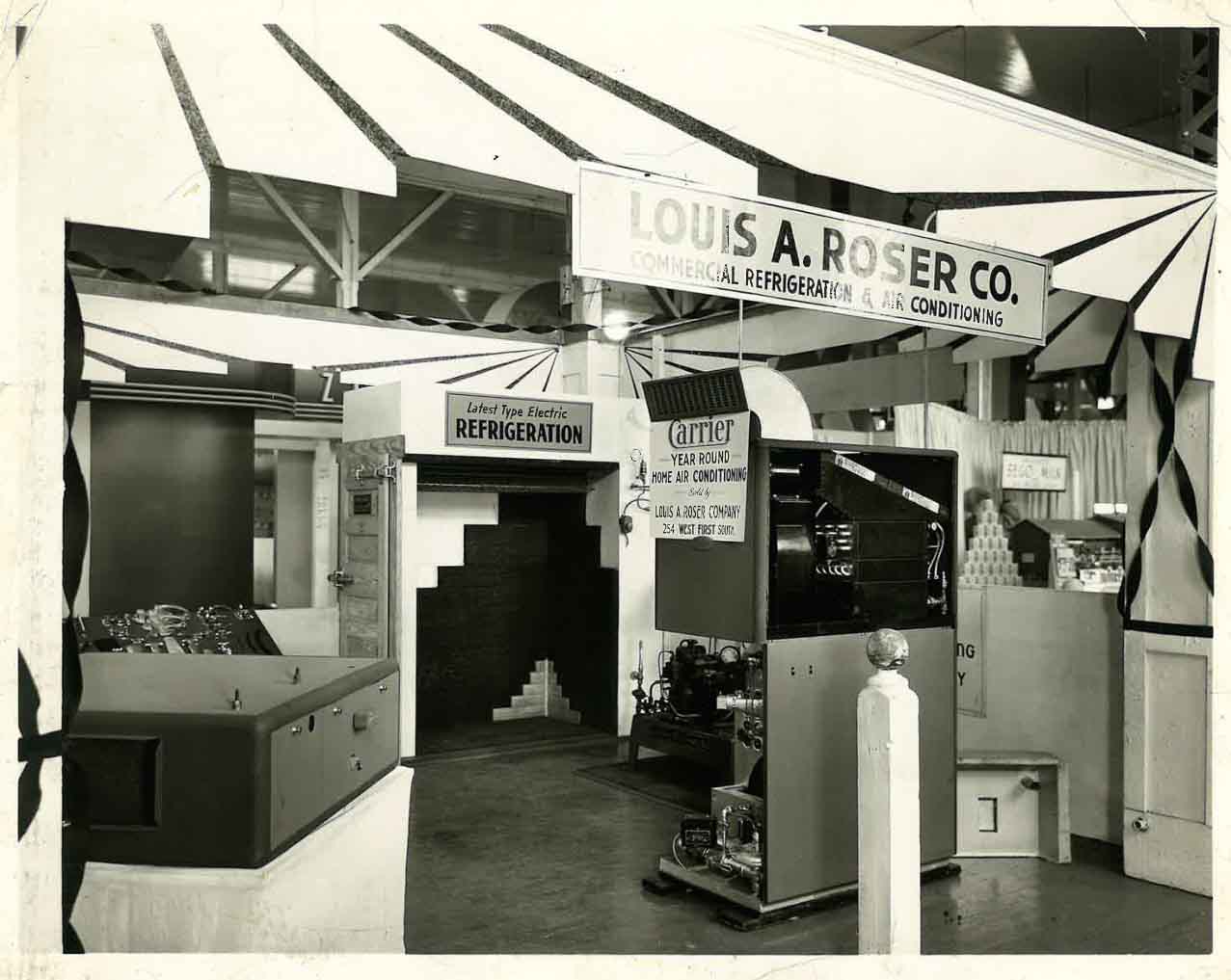
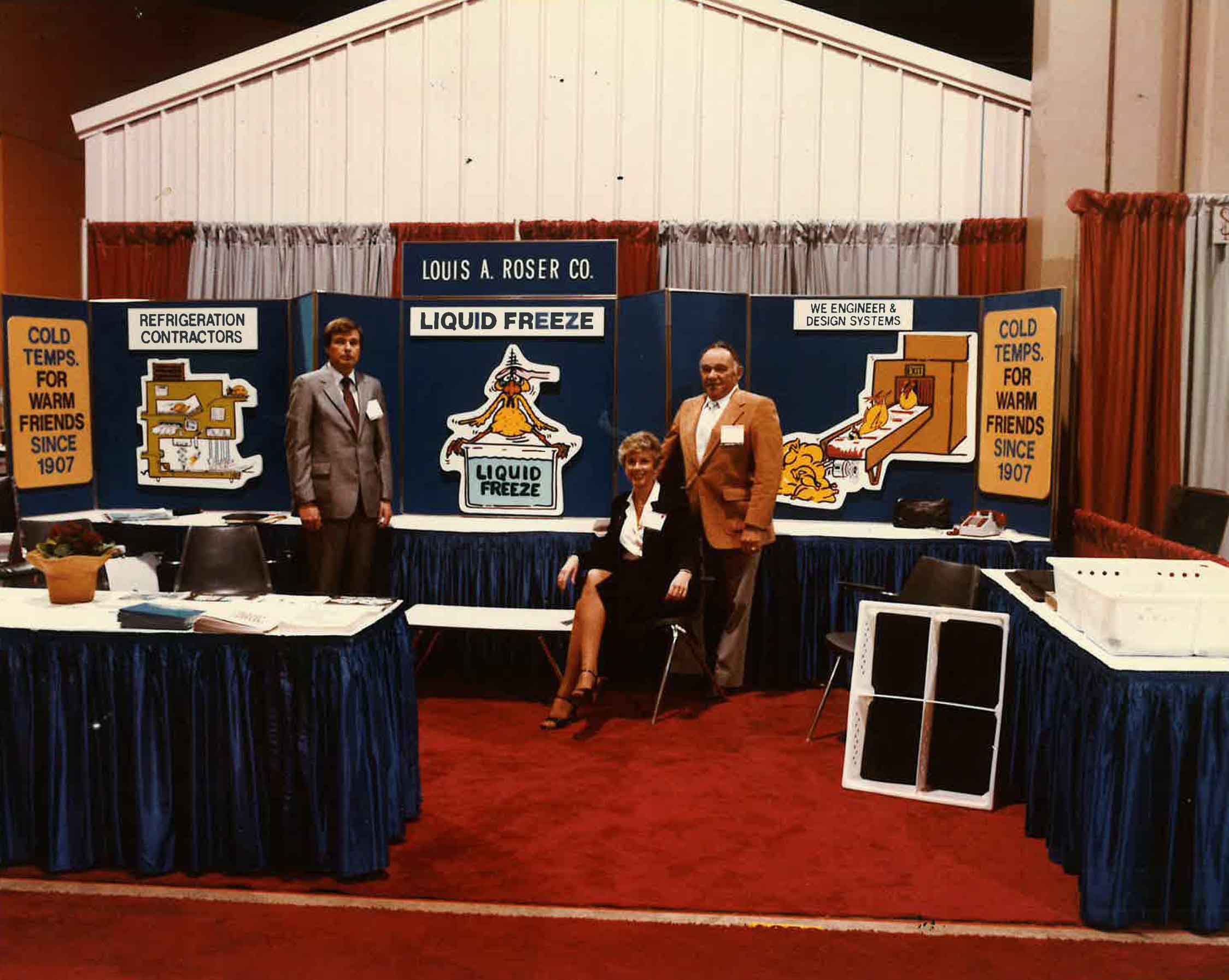
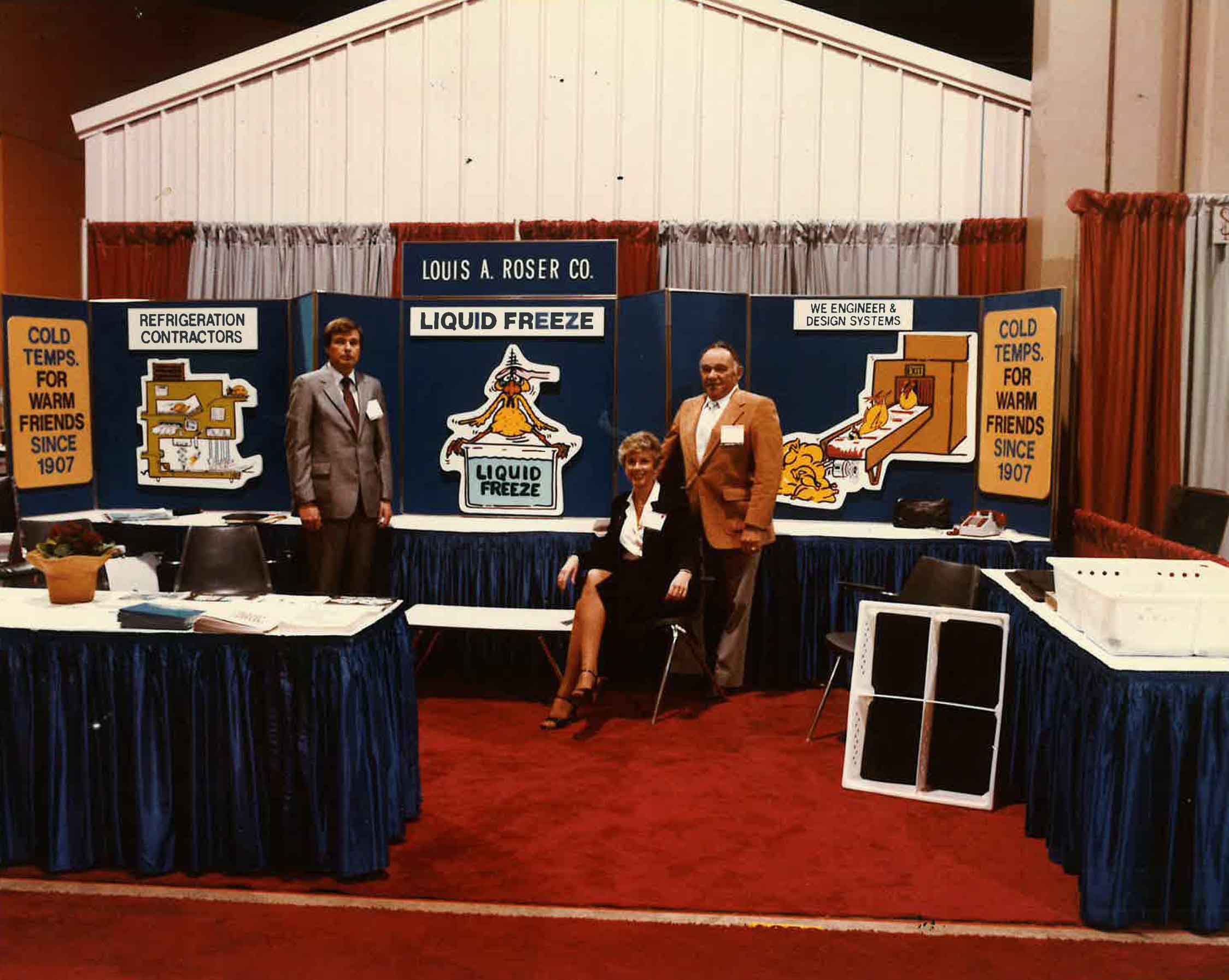
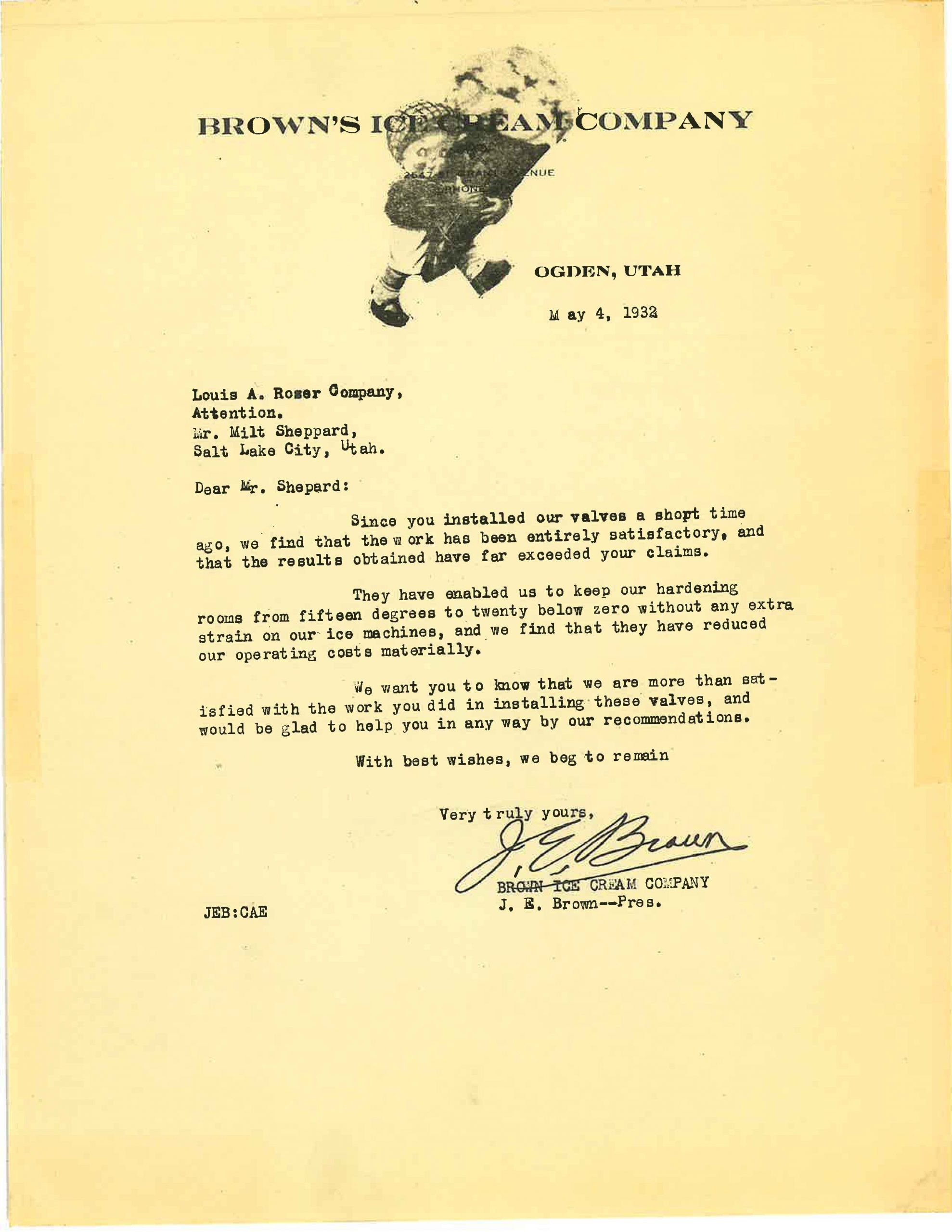
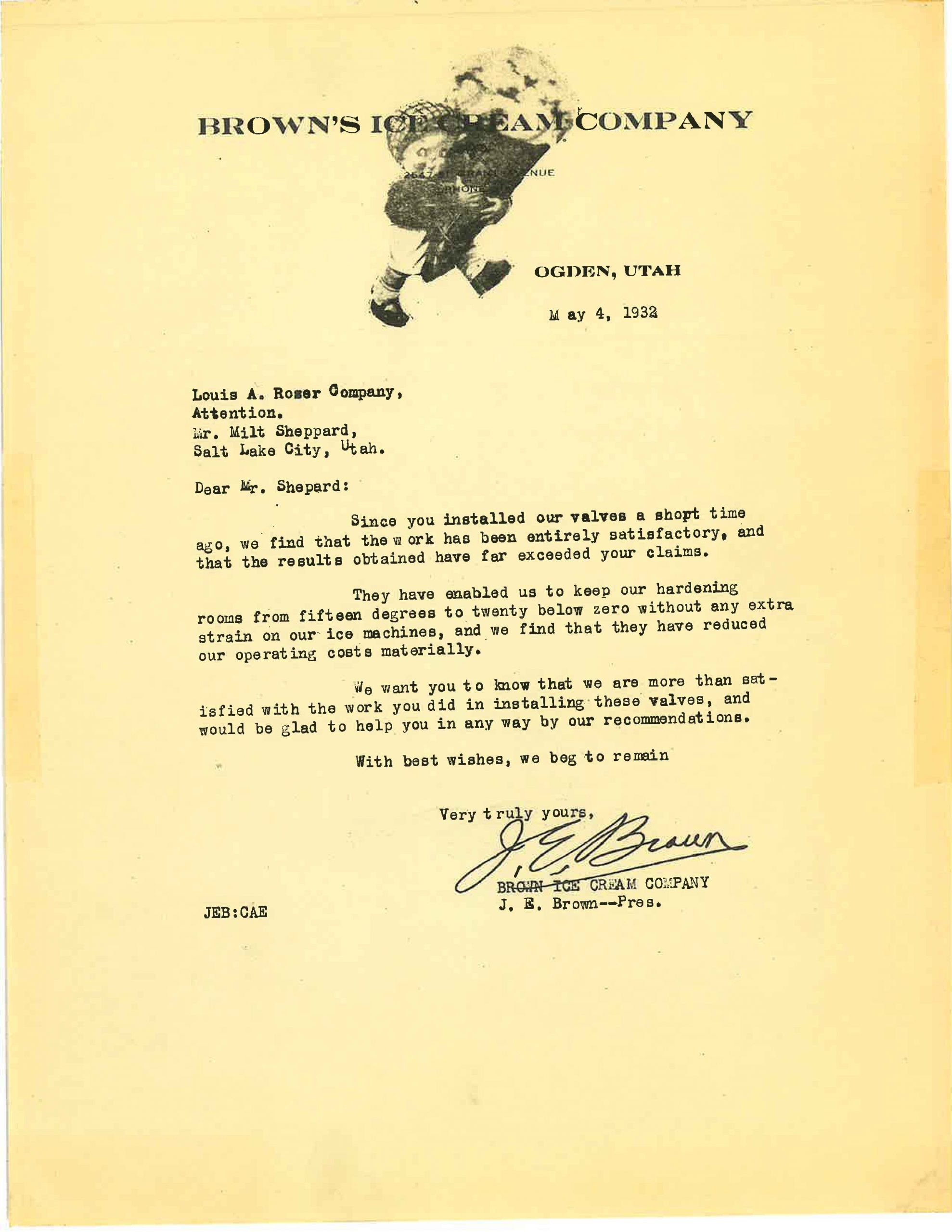
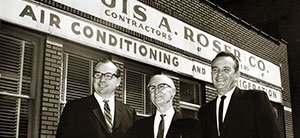
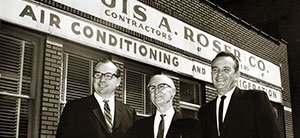
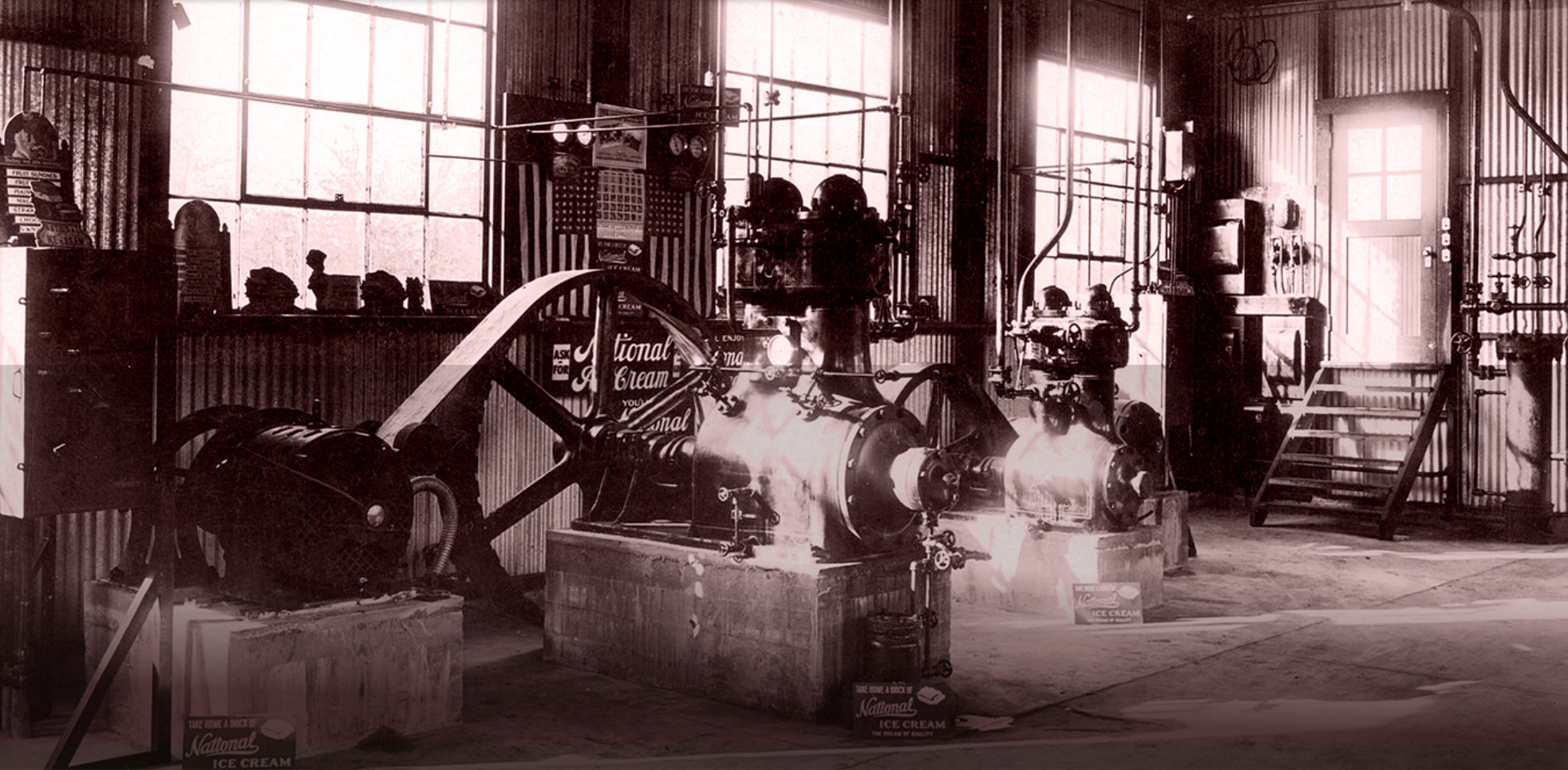
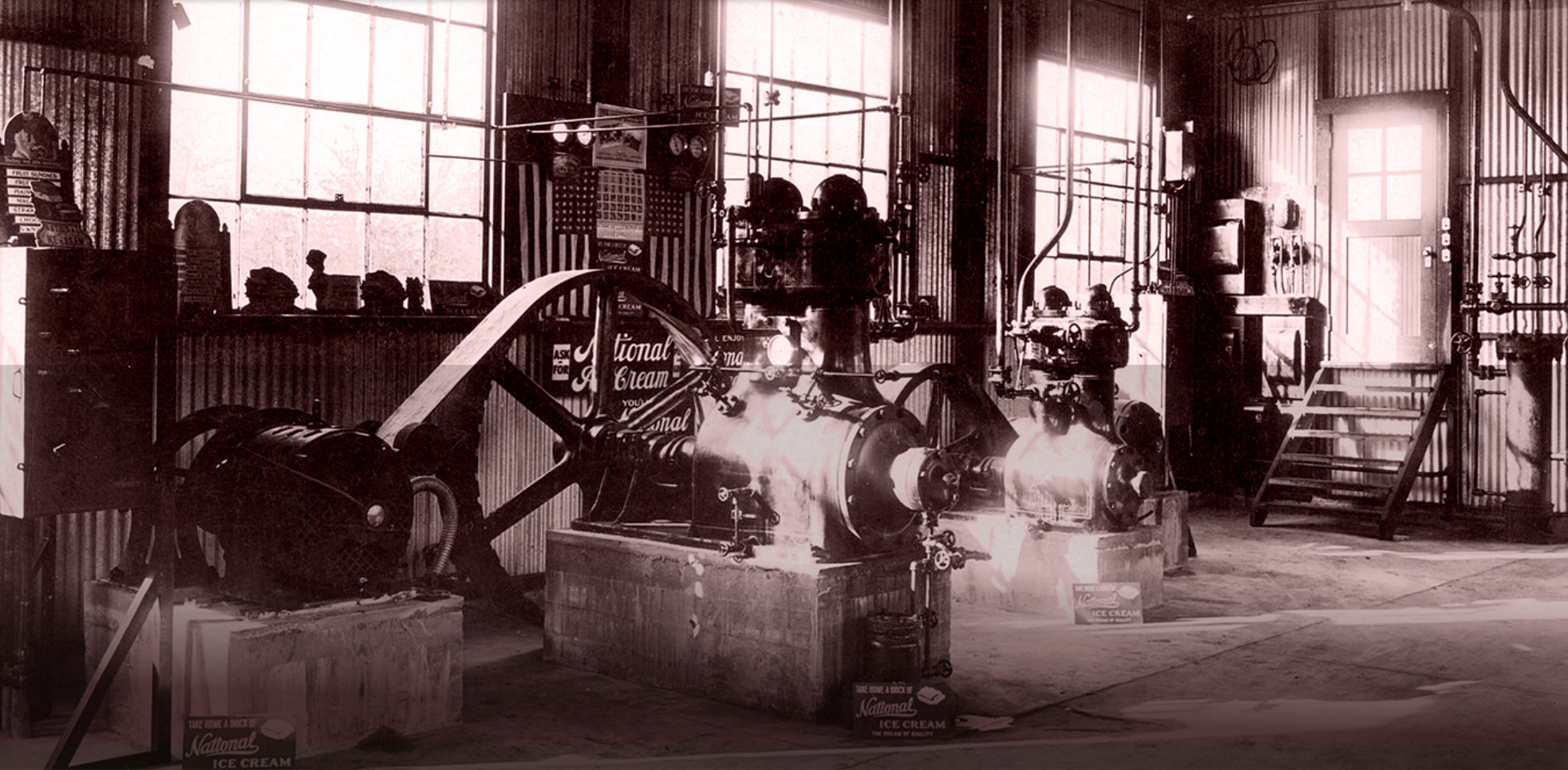
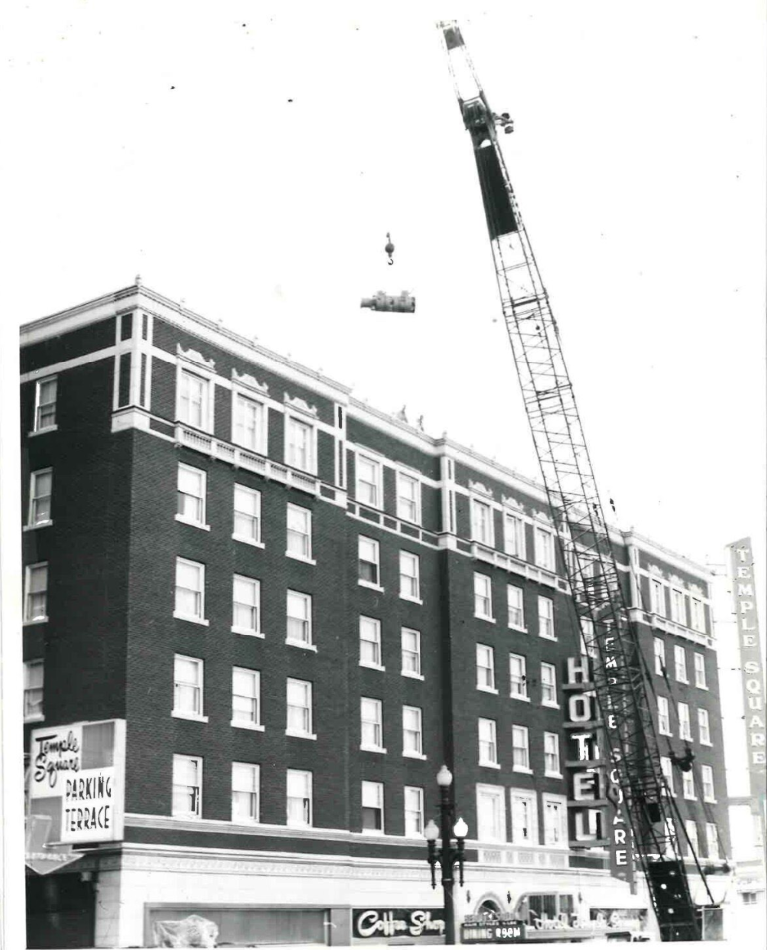
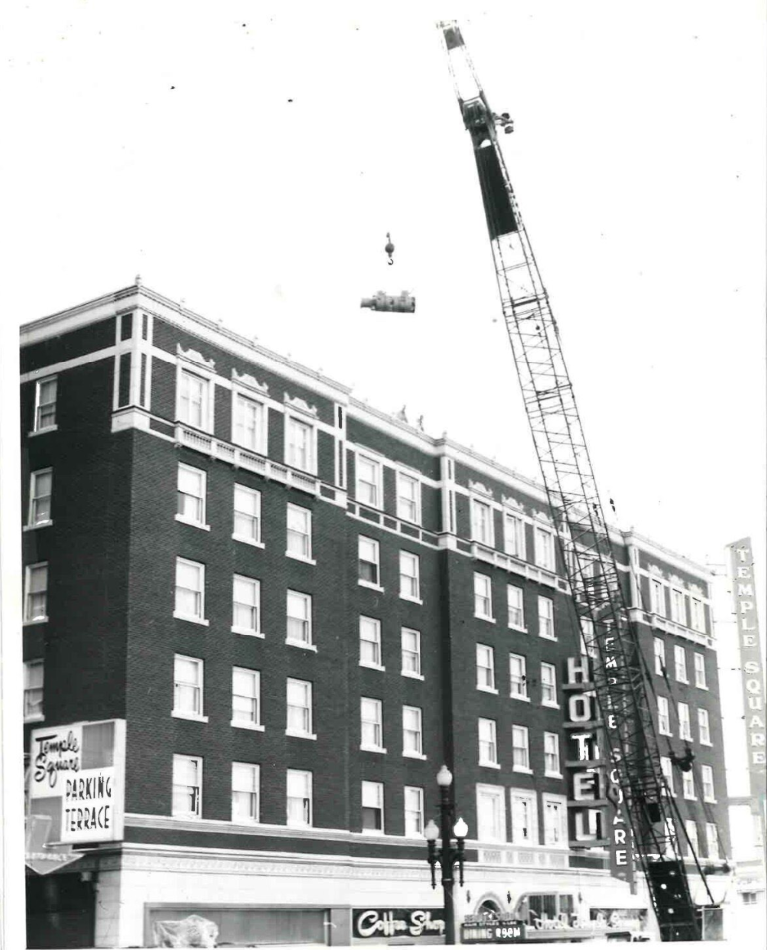
Ready to
work with us?
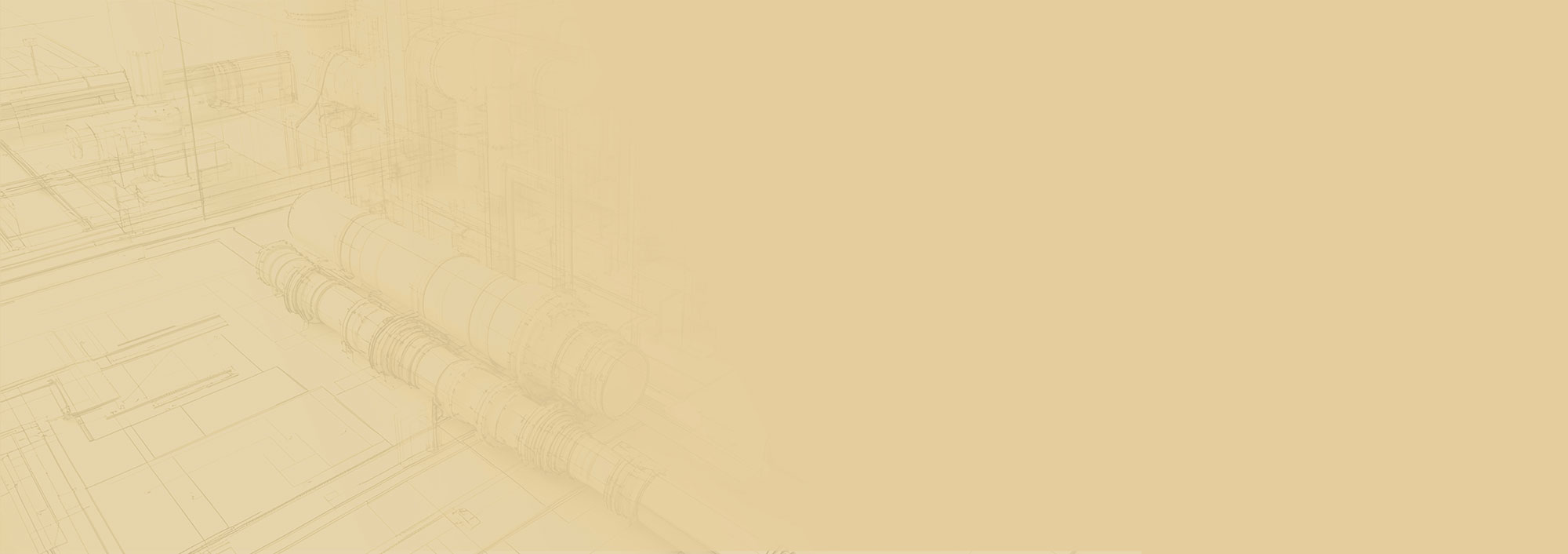